ZILMET-LMG系列计量泵在LYJY-ZS油田注水加药装置中的应用
ZILMET-LMG系列计量泵在LYJY-ZS油田注水加药装置中的应用首先让我们了解一下ZILMET-LMG系列计量泵的特点
1、重力铸造铝外壳散热性能高,整体重量轻。ZILMET-LMG系列计量泵适用于各种酸碱溶液,无毒无味。
2、采用双偏心n轴机构,运行平稳无噪音。
3、、接触介质泵头由聚氯乙烯、聚四氟乙烯和不锈钢制成。
4、由于其高性价比,它被广泛应用于对压力要求较低的水处理行业。
5、
ZILMET-LMG系列计量泵在运行或停止时,流量可任意调节,也可实现定量输出。
6、所有标准件均压入模具,易损件易于供应,价格低廉。
测量范围:0-500l/h流量:50L/h 120L/h 170L/h 240L/h 300L/h 400L/h 500l/h
ZILMET-LMG系列
计量泵的压力范围:0-1.0mpa
驱动方式:电机驱动(可采用普通电机、防爆电机、变频电机)
控制方式:手动、自动控制(可接收4-20mA信号调节流量)。LYJY-ZS油田注水加药装置设计。目前在输油管道的各种加药过程中,经常采用人工控制。仅凭储药罐上的玻璃管液位计无法准确配制所需浓度的破乳剂溶液,不能根据液位的变化自动、准确地调整破乳剂的注入量,造成水的浪费,电力和人力,以及不断增加的能源消耗。针对上述问题,研制了基于FPL-PLC的自动加水、定量加药、定时搅拌、自动倒罐的控制装置。实际运行表明,该装置不仅降低了职工劳动强度,提高了安全系数,实现了以人为本的原则,使油田工业自动化水平达到了一个新的起点,提高了现场管理水平,使生产管理更加规范化、科学化。2系统结构2.1加药装置的基本结构。加药装置包括药品储罐、计量泵、搅拌器、液位开关、控制箱及附件。在实际系统中,可以根据用户需求调整配置,以适应不同的工艺要求。图1显示了加药装置的结构。控制系统包括:两台搅拌机、一台加水电机、一台加药电机、两台加药罐、一个化学品储罐、多个电磁阀、高液位报警、低液位报警及交流接触器、热继电器、中间继电器、控制按钮、信号灯、断路器、开关等低压控制装置。2.2系统控制功能说明自动加药装置是根据加药溶液的浓度实现自动加药、自动混合、自动定量输出的自动控制系统。在设定状态下,设备不需要手动值守。可实现所需浓度溶液的自动配制和输出,并可实现远程控制,真正实现了配料、混合、加药的自动化。考虑到现场操作的需要,设有手动控制功能,在任何情况下都优先采用手动控制。(1) 手动操作前,将操作模式转到“手动”位置,打开10.2,调用“手动控制”子程序。根据控制面板上相应的按钮,可以连接相应的PLC输入点并执行相应的动作。以1号水箱为例,加水电机接通,即i0.5接通,输出继电器q0.1接通并自锁,外部交流继电器通电,加水电机开始加水。断开加水电机,即连接i0.6,断开q0.1,停止加水电机(当加水电机故障时,连接12.7,其常闭触点断开,Qo。1断开,加水电机停止运行)。接通加药电机,即10.7接通,q0.2输出继电器接通并自锁,外部交流继电器通电,加药电机开始运行。断开加药电机,即11.0连接,Qo。2断开,电机停止运行(加药电机故障时,连接13。O、 其常闭触点断开,q0.2断开,加药电机停止运行)。当混频器连接时,即i0.3连接时,输出继电器Qo。④ 通讯能力强,扩展模块丰富;⑤易于操作和掌握。根据设备的运行特点和用户的实际需要,基于S7-200 PLC控制,采用内部软继电器实现过程控制,使系统控制简单,提高了系统的稳定性和可靠性,保证了产品质量,提高了生产效率。3.2硬件电路分别在1号罐和2号罐内设计,设有高液位控制器和低液位控制器。控制器的数据信号通过导线与配电柜内的控制电路相连,实现对PLC的控制。图2显示了系统接口电路图。3.2.1搅拌机系统的搅拌轴包括传动轴本身和随轴转动的叶片。它是流体混合装置的一个子系统,混合轴是混合操作的主要部分。由于流体激振力、输入转速波动和搅拌轴偏心的影响,搅拌轴的振动有三种类型:轴向振动、扭转振动和弯曲振动。轴向振动是搅拌轴的伸长和缩短。
轴向振动的固有频率通常很高(超过3 OOo赫兹)。因此,在设计搅拌器时不考虑搅拌轴的轴向振动。由于扭振引起的搅拌轴转速波动很难观察到,其固有频率也很高。弯曲振动是轴的横向摆动。它是Z的一种有害振动形式,其固有频率低且具有破坏性。它与流体激振频率和轴转速相近,容易引起共振。因此,研究搅拌轴的弯曲振动,准确确定搅拌轴的临界转速,对于搅拌轴的设计和轴的失效预测具有重要意义。本装置设计搅拌速度为120r/min,叶片安装在距轴端100mm处,搅拌轴通过联轴器与减速机输出轴连接。螺旋叶片通常为三叶,也可以是2叶或4叶。搅拌槽叶片直径与内径之比为0.2~0.5,一般为0.33,节距与叶片直径之比为1:2。图3为混合器的结构图。3.2.2
LYJY-ZS油田注水加药装置与气力输送系统直接相连。气力输送系统的正常运行必须具备恒压条件。如果系统的压力损失过大,会增加风机的负担,甚至造成粉料堵塞,影响工作。为了尽可能降低系统的压力损失,装置设计中计量加药装置采用变螺距螺旋输送机作为压力送料气力输送装置的给料装置。装置离气力输送管道越近,螺距越小,使输送的粉末被压紧,切断漏气通道。螺旋进给装置的结构。在带衬套的铸铁壳体3中,有一段变螺距螺杆轴4,其右端通过弹性联轴器与电机5连接。当螺杆在壳体中快速旋转时,物料从上加料斗2通过螺杆通过浇口L压入物料输送管6。输送管与气力输送装置的输送管连接,物料送入气力输送系统。随着螺杆螺距从左到右逐渐减小,进入螺旋的物料被压得越来越紧,可以防止气力输送管路中的压缩空气通过螺杆泄漏出去。物料进入气力输送系统后,与压缩空气相遇,吹散,使物料加速,形成压缩空气和物料的混合物,均匀地进入气力输送系统的输送管道,在高速气流的驱动下输送物料。3.3程序设计系统程序大部分采用梯形图编制,模拟计算和输出采用功能块和语句表。梯形图直观易懂,常用RS触发器和时间继电器。在编程中,只需分析和找到sy设置和复位条件,使每个受控(PLC输出)按顺序写入即可。这样可以使程序简洁,减少编程错误的机会。
LYJY-ZS油田注水
加药装置第1次投加DFY后,自动判断投加装置为开或关状态(第1次投注后,DFY自动投加)?如果df23关闭,表示2号罐向管道内注入化学品时,1号罐可以给水、加药、搅拌;如果df23开启,则表示1号罐向管道内注入化学品,2号罐可以给水、加药、搅拌)。加药箱Z液位不高,加药箱水位不高,加药箱水位不高,加药箱水位不高。当加药罐液位达到Z高液位时,传感器发出信号,加水电机停止,进水电磁阀关闭,加水过程结束。之后,加药电机和搅拌机同时启动。定时器KF3和kf4启动。经过一定延时后,加药电机先停止,搅拌一定时间后搅拌机停止。加药和混合过程完成。1号罐加水、加药、搅拌完成,等待。在2号罐加药过程中,当Z低液位报警时,发出信号请求,关闭2号罐加药阀df24,打开1号罐加药阀df23,1号罐向管道内注药,实现自动加水,2号罐定量加药定时搅拌。完成浇注过程。图5为加药装置的程序流程图,图6为控制系统的梯形图。结论在LYJY-ZS油田注水加药装置的系统设计中,将各环节的工作信息传送给PLC控制系统,使加药系统自动运行,药液浓度恒定,加药准确。实现了加药罐的全部自动化,大大提高了工作效率,减轻了工人的劳动强度,减少了化学品对人体的危害。同时,该装置还具有结构紧凑、配置丰富、安装简单、可靠性高等优点。
LYJY-ZS油田注水加药装置是一种自动化程度高的药剂加药系统。本文旨在寻找一种具有更高实用价值和更广阔应用前景的产品,实现环境效益和经济效益的统一。以上是ZILMET-LMG系列计量泵在LYJY-ZS油田注水加药装置中的应用,以及LYJY-ZS油田注水加药装置的工作原理和工艺流程。欢迎更多计量泵和注水加药装置与上海龙亚技术部洽谈。
Application of ZILMET-LMG series metering pump in water injection and dosing device of LYJY-ZS Oilfield
First of all, let's understand the characteristics of ZILMET-LMG series metering pump
1. Gravity casting aluminum shell has high heat dissipation performance and light weight. ZILMET-LMG series metering pump is suitable for all kinds of acid-base solution, non-toxic and tasteless.
2. Using double eccentric n-axis mechanism, it runs stably without noise.
3. Contact medium pump head is made of PVC, PTFE and stainless steel.
4. Because of its high cost performance, it is widely used in water treatment industry with low pressure requirements.
5. When ZILMET-LMG series metering pump is running or stopping, the flow can be adjusted arbitrarily, and the quantitative output can also be realized.
6. All standard parts are pressed into the mould, and the wearing parts are easy to supply and the price is low.
Measurement range: 0-500l / h flow: 50L / h 120L / h 170L / h 240L / h 300L / h 400L / h 500L / h
Pressure range: 0-1.0mpa drive mode: motor drive (ordinary motor, explosion-proof motor and frequency conversion motor can be used)
Control mode: manual and automatic control (can receive 4-20mA signal to adjust flow). Design of water injection and dosing device for LYJY-ZS oilfield. At present, manual control is often used in various dosing processes of oil pipeline. The glass tube liquid level gauge on the drug storage tank can not accurately prepare the required concentration of demulsifier solution, and can not automatically and accurately adjust the injection amount of demulsifier according to the change of liquid level, resulting in waste of water, power and manpower, and increasing energy consumption. In view of the above problems, a control device based on fpl-plc is developed for automatic water adding, quantitative dosing, timing stirring and automatic tank pouring. The actual operation shows that the device not only reduces the labor intensity of workers, improves the safety factor, realizes the principle of people-oriented, makes the Oilfield Industrial automation level reach a new starting point, improves the field management level, and makes the production management more standardized and scientific. 2 system structure 2.1 basic structure of dosing device. The dosing device includes drug storage tank, metering pump, agitator, liquid level switch, control box and accessories. In the actual system, the configuration can be adjusted according to the needs of users to adapt to different process requirements. Figure 1 shows the structure of the dosing device. The control system includes two mixers, one water adding motor, one dosing motor, two dosing tanks, one chemical storage tank, multiple solenoid valves, high level alarm, low level alarm and AC contactor, thermal relay, intermediate relay, control button, signal lamp, circuit breaker, switch and other low-voltage control devices. 2.2 system control function description the automatic dosing device is an automatic control system which can realize automatic dosing, automatic mixing and automatic quantitative output according to the concentration of dosing solution. In the set state, the equipment does not need to be on duty manually. It can realize the automatic preparation and output of the required concentration solution, and realize the remote control, so as to realize the automation of batching, mixing and dosing. Considering the need of field operation, manual control function is set, and manual control is preferred in any case. (1) Before manual operation, turn the operation mode to "manual" position, open 10.2, and call "manual control" subroutine. According to the corresponding buttons on the control panel, the corresponding PLC input points can be connected and corresponding actions can be executed. Take No.1 water tank as an example, the water adding motor is connected, i.e. i0.5 is connected, the output relay q0.1 is connected and self-locking, the external AC relay is powered on, and the water adding motor starts to add water. Disconnect the water adding motor, i.e. connect i0.6, disconnect q0.1, and stop the water adding motor (when the water adding motor fails, connect 12.7, its normally closed contact is open, Qo. 1 is disconnected, and the water adding motor stops running). Switch on the dosing motor, that is, 10.7 is on, q0.2 output relay is on and self-locking, the external AC relay is powered on, and the dosing motor starts to run. Disconnect the dosing motor, i.e. 11.0 connection, Qo. 2 is disconnected and the motor stops running (when the dosing motor fails, connect 13. O. The normally closed contact is open, q0.2 is disconnected, and the dosing motor stops running). When the mixer is connected, i.e. i0.3 is connected, the output relay Qo. ④ It is easy to operate and master. According to the operation characteristics of the equipment and the actual needs of users, based on S7-200 PLC control, the internal soft relay is used to realize process control, which makes the system control simple, improves the stability and reliability of the system, ensures the product quality and improves the production efficiency. 3.2 hardware circuit is designed in No.1 tank and No.2 tank respectively, with high level controller and low level controller. The data signal of the controller is connected with the control circuit in the power distribution cabinet through the wire to realize the control of PLC. Figure 2 shows the system interface circuit diagram. 3.2.1 the mixing shaft of the mixer system includes the drive shaft itself and the blades rotating with the shaft. It is a subsystem of fluid mixing device, and mixing shaft is the main part of mixing operation. Due to the influence of fluid exciting force, input speed fluctuation and eccentricity of mixing shaft, there are three types of vibration of mixing shaft: axial vibration, torsional vibration and bending vibration. Axial vibration is the elongation and shortening of mixing shaft.
The natural frequency of axial vibration is usually very high (more than 3 OOo Hz). Therefore, the axial vibration of mixing shaft is not considered in the design of agitator. It is difficult to observe the speed fluctuation of the mixing shaft caused by torsional vibration, and its natural frequency is also very high. Bending vibration is the lateral swing of the shaft. It is a harmful vibration form of Z, with low natural frequency and destructive. It is similar to the frequency of fluid excitation and shaft speed, and it is easy to cause resonance. Therefore, it is of great significance to study the bending vibration of the mixing shaft and determine the critical speed of the mixing shaft accurately for the design of the mixing shaft and the failure prediction of the shaft. The mixing speed of the device is designed to be 120r / min, the blade is installed at the position of 100 mm from the shaft end, and the mixing shaft is connected with the output shaft of the reducer through the coupling. Spiral leaves are usually trifoliate, but can also be 2-or 4-leaved. The ratio of blade diameter to inner diameter is 0.2 ~ 0.5, generally 0.33, and the ratio of pitch to blade diameter is 1:2. Fig. 3 shows the structure of the mixer. 3.2.2 metering dosing device metering dosing device is directly connected with pneumatic conveying system. The normal operation of pneumatic conveying system must have constant pressure condition. If the pressure loss of the system is too large, it will increase the burden of the fan, and even cause powder blockage, affecting the work. In order to reduce the pressure loss of the system as much as possible, the variable pitch screw conveyor is used as the feeding device of the pneumatic conveying device. The closer the device is to the pneumatic conveying pipeline, the smaller the pitch is, so that the powder transported is compressed and the air leakage channel is cut off. Structure of screw feed device. In the cast iron housing 3 with bushing, there is a section of variable pitch screw shaft 4, and its right end is connected with the motor 5 through an elastic coupling. When the screw rotates rapidly in the shell, the material is pressed into the material conveying pipe 6 through the screw through the gate L from the top feeding hopper 2. The conveying pipe is connected with the conveying pipe of the pneumatic conveying device, and the materials are sent into the pneumatic conveying system. As the screw pitch gradually decreases from left to right, the material entering the screw is pressed more and more tightly, which can prevent the compressed air in the pneumatic conveying pipeline from leaking out through the screw. After the material enters the pneumatic conveying system, it meets with the compressed air and blows away, which accelerates the material to form a mixture of compressed air and material, and evenly enters the conveying pipeline of the pneumatic conveying system to transport materials under the driving of high-speed air flow. 3.3 most of the program design system programs are compiled by ladder diagram, and function block and statement table are used for simulation calculation and output. Ladder diagram is intuitive and easy to understand. RS trigger and time relay are commonly used. In programming, it is only necessary to analyze and find sy setting and reset conditions, so that each controlled (PLC output) can be written in sequence. This can make the program concise and reduce the chance of programming errors.
After the first dosing of dfy in LYJY-ZS oilfield water injection and dosing device, it can automatically judge whether the dosing device is on or off (after the first injection, dfy is automatically added)? If df23 is closed, it means that when No. 2 tank injects chemicals into the pipeline, No. 1 tank can supply water, add chemicals and mix; if df23 is on, it means that No. 1 tank can inject chemicals into the pipeline, and No. 2 tank can supply water, add chemicals and mix). The liquid level of dosing tank Z is not high, the water level of dosing tank is not high, the water level of dosing tank is not high, and the water level of dosing tank is not high. When the liquid level of the dosing tank reaches Z high level, the sensor sends a signal, the water adding motor stops, the water inlet solenoid valve is closed, and the water adding process is finished. After that, the dosing motor and mixer start at the same time. Timer KF3 and kf4 are started. After a certain delay, the dosing motor stops first, and the mixer stops after mixing for a certain time. The process of dosing and mixing was completed. Add water, add medicine and stir in No.1 tank, wait. During the dosing process of No.2 tank, when Z low liquid level alarm is given, a signal request is sent to close the dosing valve df24 of No.2 tank and open the dosing valve df23 of No.1 tank. The No.1 tank injects chemicals into the pipeline to realize automatic water adding, and the dosing and mixing of No.2 tank are carried out at fixed time. Complete the pouring process. The ladder diagram of dosing system is 6. Conclusion in the system design of LYJY-ZS oilfield water injection and dosing device, the working information of each link is transmitted to the PLC control system, so that the dosing system can run automatically, the concentration of liquid medicine is constant and the dosing is accurate. The automation of dosing tank is realized, the work efficiency is greatly improved, the labor intensity of workers is reduced, and the harm of chemicals to human body is reduced. At the same time, the device has the advantages of compact structure, rich configuration, simple installation and high reliability. LYJY-ZS oilfield water injection and dosing device is a kind of high automation reagent dosing system. The purpose of this paper is to find a product with higher practical value and wider application prospect, so as to realize the unification of environmental and economic benefits. The above is the application of ZILMET-LMG series metering pump in LYJY-ZS oilfield water injection and dosing device, as well as the working principle and process flow of LYJY-ZS oilfield water injection and dosing device. Welcome more metering pumps and water injection dosing devices to negotiate with Shanghai Longya technology department.
地址:上海市松江区小昆山经济区崇南公路435弄20号
电话:021-33510117
021-33510177
021-33510187
热线:4OO-OO1-5655
传真:021-39160355
邮箱:shlongya@163.com


销售部微信:
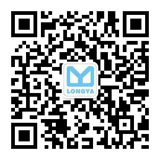